HDPE Heat Insulation Pipe Extrusion Line
Main Technical Parameter
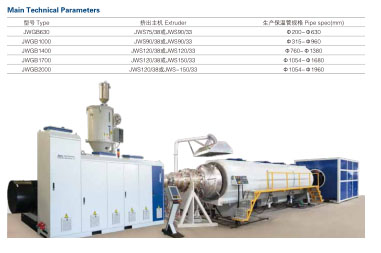
Performance and features
The insulation pipe production line is designed with a special PE insulation pipe mold, the extrusion pressure is stable, and the thickness of the thin-walled pipe is uniform. The extrusion speed is fast, the output of the blown type is greatly improved, the surface is brighter, and the operation automation is high.
HDPE pipe is a flexible plastic pipe made of thermoplastic high-density polyethylene widely used for low-temperature fluid and gas transfer. In recent times, HDPE pipes got their extensive uses for carrying potable water, hazardous wastes, various gases, slurry, firewater, stormwater, etc. The strong molecular bond of HDPE pipe materials helps it to use for high-pressure pipelines. Polyethylene pipes have a long and distinguished service history for gas, oil, mining, water, and other industries. Due to its low weight and high corrosion resistance, the HDPE pipe industry is growing tremendously. In the year 1953, Karl Ziegler and Erhard Holzkamp discovered high-density polyethene (HDPE). HDPE pipes can work satisfactorily in a wide temperature range of -2200 F to +1800 F. However, the use of HDPE Pipes is not suggested when the fluid temperature exceeds 1220 F (500 C).
HDPE pipes are made by the polymerization of ethylene, a by-product of oil. Various additives (stabilizers, fillers, plasticizers, softeners, lubricants, colorants, flame retardants, blowing agents, crosslinking agents, ultraviolet degradable additives, etc.) are added to produce the final HDPE pipe and components. HDPE pipe lengths are made by heating the HDPE resin. It is then extruded through a die, which determines the diameter of the pipeline. The Pipe wall thickness is determined by a combination of the die size, speed of the screw, and the speed of the haul-off tractor. Usually, 3-5% carbon black is added to HDPE to make it UV resistant, which turns HDPE pipes into black in color. Other color variants are available but usually not used frequently. Coloured or striped HDPE pipe is usually 90-95% black material, where a colored stripe is provided on 5% of the outside surface.