When traditional production lines struggle with efficiency and quality, JWELL Machinery revolutionizes the industry with fully automated sheet extrusion lines! From refrigerators to sanitary ware manufacturing, our equipment empowers every sheet with cutting-edge technology + intelligent automation!
JWELL Machinery offers domestically leading production lines for refrigerator panels and sanitary ware panels made of ABS, HIPS, and PMMA, featuring high output, low energy consumption, and high intelligence. The production lines are equipped with a centralized automatic feeding system. The screw rotation speed automatically forms a closed - loop with the pressure, ensuring stable die discharge during the production process. The gaps of the three - roll servo motors are automatically adjusted, and automatic positioning is achieved through the control method corresponding to the movement position, with high precision. Based on products of different models and specifications, functions such as online trimming, cutting, waste edge collection, and edge - free trimming are realized. There are also automatic robotic stacking and large - diameter winding machines, achieving a high degree of automated production. This significantly reduces production costs and improves product quality, making the production lines highly popular among customers.
Four Core Technologies
Automatic feeding system: JWELL Machinery has meticulously crafted a sheet extrusion production line that holds an absolute leading position in China. It features remarkable advantages such as high output, low energy consumption, and high intelligence. Notably, it is equipped with an advanced centralized automatic feeding system. This system can accurately and efficiently convey various raw materials according to the real-time needs of the production line, effectively avoiding errors and delays that may occur in manual feeding. It not only greatly improves the overall production efficiency but also further ensures the stability and continuity of the production process, laying a solid foundation for enterprises to achieve large-scale and high-quality sheet production.
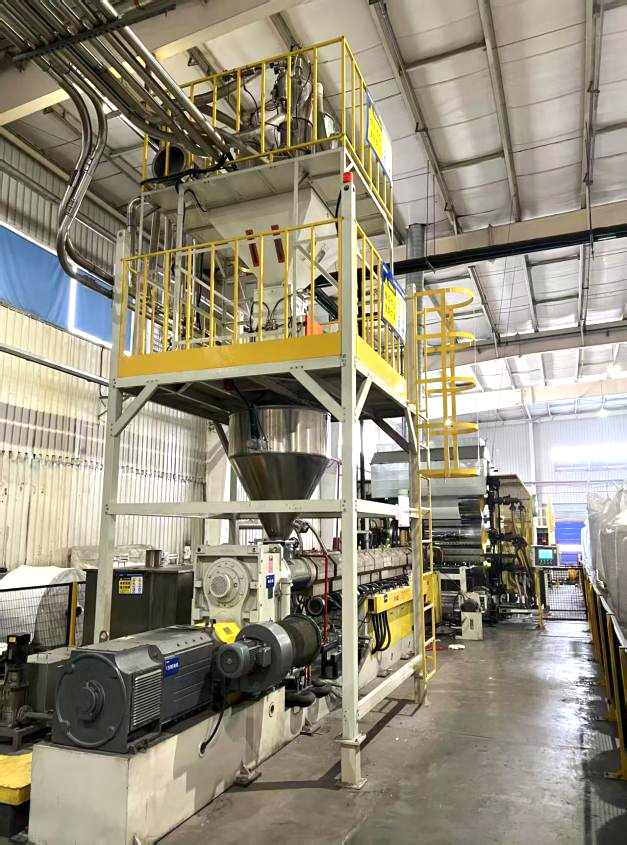
Automatic closed-loop control of screw rotation speed: In the sheet extrusion production line, the automatic closed-loop system for screw speed plays a crucial role. During production, the pressure sensor continuously monitors the die discharge pressure. The data is then fed back to the control system, which automatically adjusts the screw speed. When the pressure is high, the screw speed decreases accordingly; when the pressure is low, the speed increases. This ensures stable die discharge at all times, significantly improving product quality and production efficiency.
Automatic adjustment of the three-roll servo motor:In the JWELL Machinery sheet extrusion production line, the automatic adjustment system of the three-roll servo motor performs outstandingly. This system can intelligently and precisely adjust the gaps between the three-roll servo motors automatically according to the requirements of the production process. During the adjustment process, it uses advanced motion-corresponding position control technology. The motors can automatically position themselves to the desired positions according to the preset program, with extremely high positioning accuracy. This not only ensures the dimensional accuracy and surface flatness of the sheet during the rolling and forming process but also greatly improves the automation level and production efficiency of the production line, helping enterprises produce higher-quality sheet products
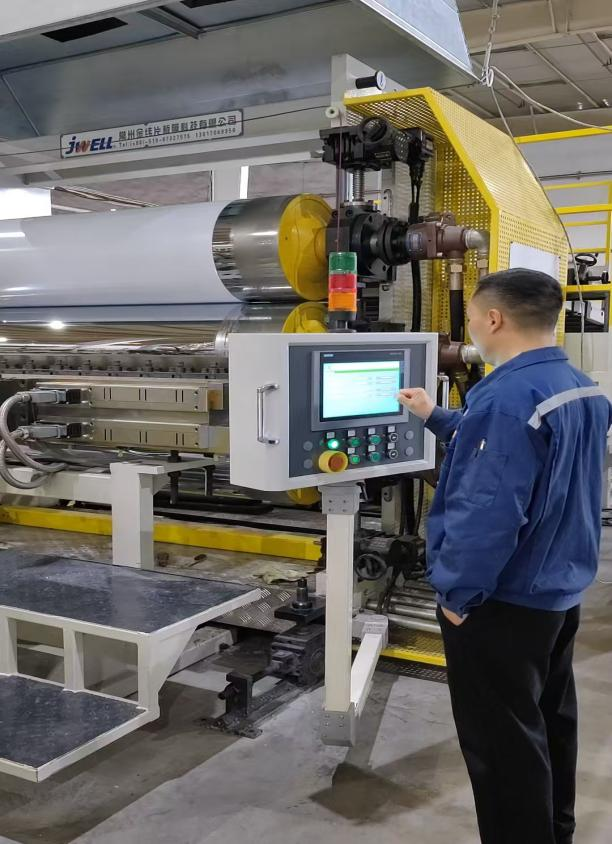
Diverse automation functions:In the sheet extrusion production line of JWELL Machinery, the automation functions demonstrate rich diversity. During production, the system can accurately perform trimming and cutting operations according to different product specifications, and simultaneously complete waste edge collection. For some special products, the edge-free trimming function can be achieved, reducing processing procedures. At the same time, it is equipped with high-performance robotic arms for automatic stacking, orderly stacking finished products, and large-diameter winding machines for efficient processing of coils. The whole process is highly automated. This not only greatly reduces production costs but also significantly improves product quality, creating greater value for enterprises.
Main technical specification
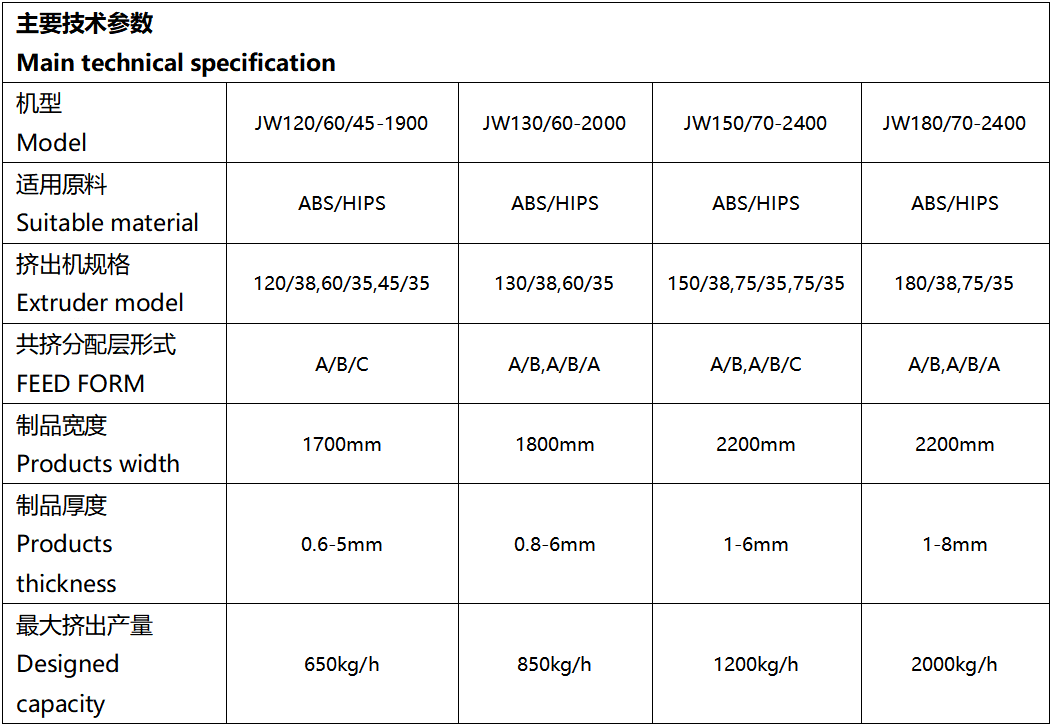
Multi-Industry Applications
In modern industrial production, sheets play an important role due to their wide range of applications. Sanitary ware sheets, as a key material in the bathroom field, are widely used in the manufacturing of bathtubs, shower rooms, steam rooms, and washbasins, helping to create a comfortable and durable bathroom space. Advertising sheets are active in various commercial and public scenarios, such as directional signs, name tags, machine signs, as well as advertising decoration and interior decoration, attracting the attention of the audience through exquisite presentation. Luggage sheets, with their excellent characteristics, are the ideal choice for manufacturing various luggage such as trolleys, suitcases, and casual bags, providing convenience for travel. Automotive sheets have diverse uses in the automotive industry, covering car roofs, instrument panels, seat backrests, door panels, window frames, and even the outer shells of motorcycles, ATVs, mobility scooters, golf carts, etc., ensuring the safety and aesthetics of vehicles.
Refrigerator Panels
Door liners, drawers with -30°C impact resistance, meeting Haier/Midea standards!
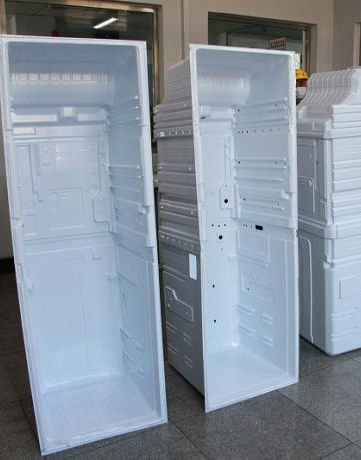
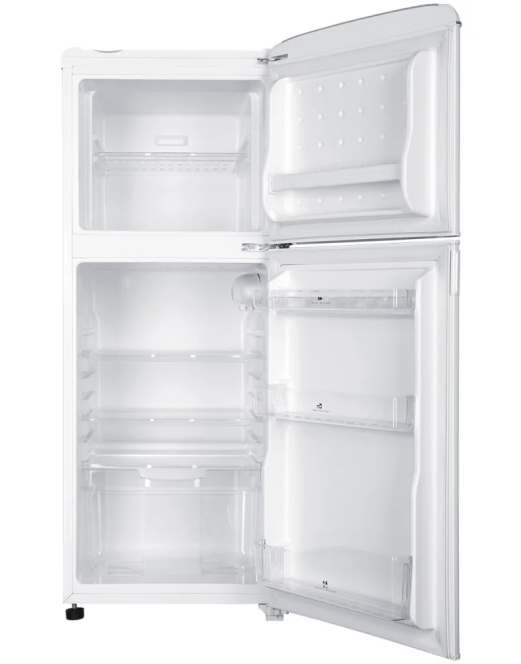
Sanitary Ware
Seamless bathtub/shower molding, 0 leakage & high-gloss finish
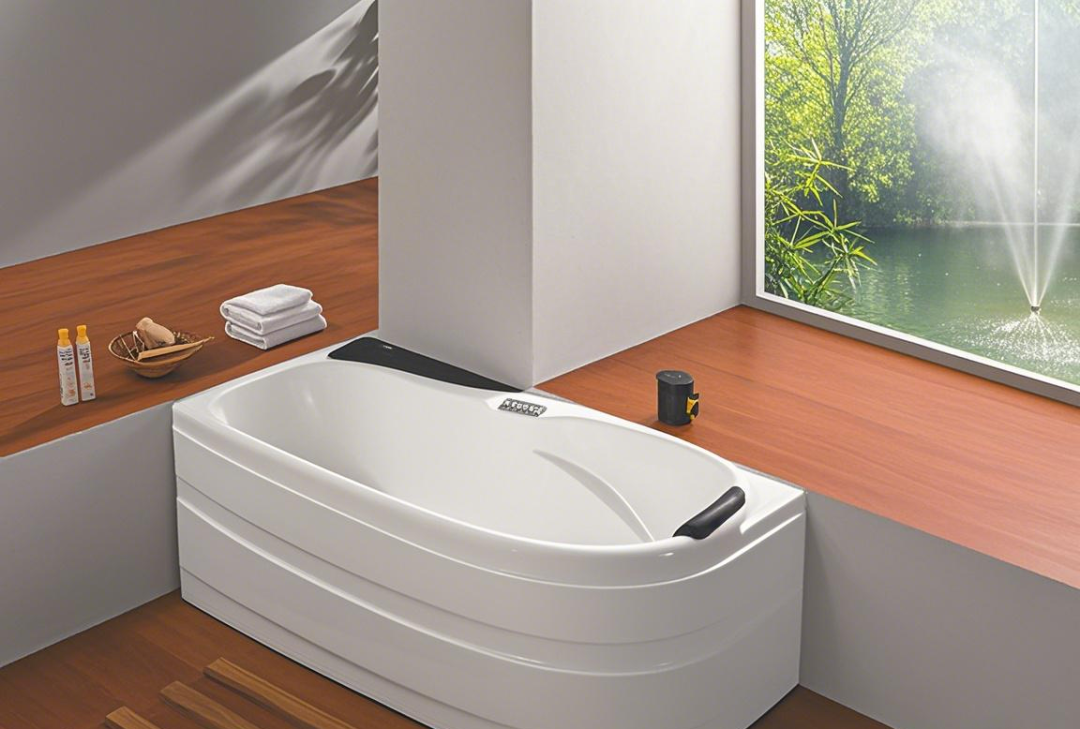
Automotive Components
UV-resistant dashboards, roof panels with metal-like strength
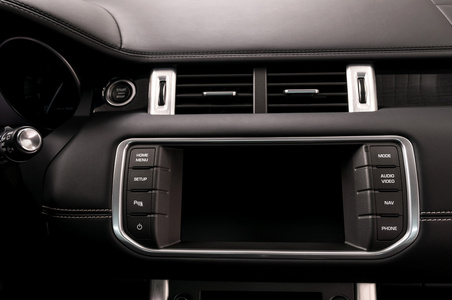
Luggage/Advertising Boards
99.8% yield rate with 3s laser trimming
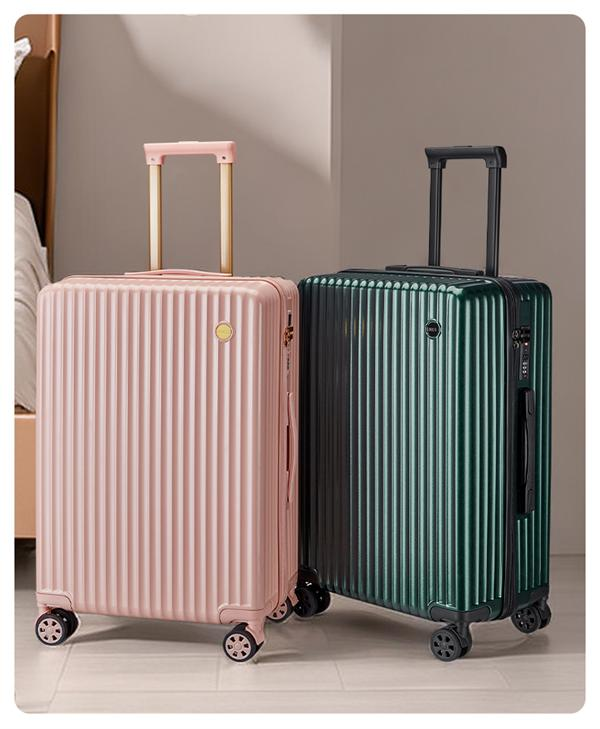
Summarize
Jwell Machinery empowers various industries in all aspects with these leading technologies, firmly establishing a new benchmark in the field of intelligent sheet manufacturing, and injecting the impetus for the entire industry to stride towards a brand-new intelligent future.
Post time: Apr-11-2025