Twin-screw extruders are the workhorse machines in the compounding field, and their superior performance and customizability are the advantages of their position. It can combine different additives and fillers to achieve different pellet shapes and properties with different performance.
While a variety of additives and fillers can be processed for extrusion, some methods of obtaining these products can also lead to contamination issues and low flow or low pressure in many areas throughout the barrel.
In a continuous process like extrusion, contamination can have an adverse effect. Purging in extrusion tends to be more challenging than other processes, and twin-screw extruders face greater challenges because the system is more complex than a single-screw extruder.
First, let's take a look at the cleaning methods of twin-screw extruders.
Resin cleaning method:
Using polyester resin or epoxy resin for cleaning is generally used for cleaning new equipment or after the extruder has been used for a period of time, because some materials remain on the screw or barrel and gel, the material extrusion speed slows down, and the color difference of the color change variety is large. This method can be used. Today, with the highly developed commodity economy, there is no shortage of various screw cleaners (screw cleaning materials) on the market, most of which are expensive and have different effects.
Whether to use commercial cleaners depends on different manufacturers and production conditions; plastic processing companies can also use different resins as screw cleaning materials according to their own production conditions, which can save a lot of expenses for the unit.
The first step in cleaning the screw is to turn off the feed plug, that is, to close the feed port at the bottom of the hopper; then reduce the screw speed to 15-25r/min and maintain this speed until the melt flow at the front end of the die stops flowing. The temperature of all heating zones of the barrel should be set at 200°C. Once the barrel reaches this temperature, start cleaning immediately.
Depending on the extrusion process (it may be necessary to remove the die to reduce the risk of excessive pressure at the front end of the extruder), cleaning must be done by one person: the operator observes the screw speed and torque from the control panel, and observes the extrusion pressure to ensure that the system pressure is not too high. During the whole process, the screw speed should be kept within 20r/min. In the application of low-pressure die heads, do not remove the die head for cleaning first. Stop and remove the die head immediately when the extrudate is completely converted from processing resin to cleaning resin, and then restart the screw (speed within 10r/min) to allow the residual cleaning resin to flow out.
Disassembly guide:
1. Manually add washing material from the discharge port until the color of the extruded material strip is the same as that of the washing material pellets, stop feeding, empty the material, and stop the rotation of the twin-screw extruder screw;
2. Open the screw extruder die head and start cleaning;
3. Turn the twin-screw extruder screw and remove the orifice plate to discharge the residual washing material in the barrel and clean the orifice plate;
4. Stop and pull out the screw to observe whether it is cleaned, and manually remove the residual material on the screw. Reinstall the screw; add new material to flush the residual washing material in the barrel and stop the screw rotation;
- Install the orifice plate and die head of the twin-screw extruder to complete the cleaning operation of the twin-screw extruder.
Fire-baked cleaning method:
Using fire or roasting to remove the plastic fixed on the screw is the most common and effective method for plastic processing units. Use a blowtorch to clean the screw immediately after use, because at this time the screw carries heat from the processing experience, so the screw The heat distribution is still uniform. But never use an acetylene flame to clean the screw. The temperature of acetylene flame can reach 3000°C. Using acetylene flame to clean the screw will not only destroy the metal properties of the screw, but also significantly affect the mechanical tolerance of the screw.
If the acetylene flame turns into a persistent blue color when baking a certain part of the screw, it means that the metal structure of this part of the screw has changed, which will lead to a reduction in the wear resistance of this part, and even the occurrence of abrasion between the anti-wear layer and the matrix. Metal peeling. In addition, local heating with an acetylene flame will also cause overheating on one side of the screw, causing the screw to bend. Most screws are made of 4140.H.T. steel and have very tight tolerances, generally within 0.03mm.
The straightness of the screw is mostly within 0.01mm. When the screw is baked and cooled by the acetylene flame, it is usually difficult to return to the original straightness. Correct and effective method: Use a blowtorch to clean the screw immediately after use. Because the screw carries heat from the processing process at this time, the heat distribution of the screw is still uniform.
Water washing method:
Screw washing: The fully automatic screw washing machine uses the kinetic energy of water rotation and the reaction force of the screw rotation to achieve 360-degree stripping without dead angles. It has high working efficiency and does not damage the physical structure of the screw. It realizes new screw cleaning technology in an environmentally friendly, efficient and energy-saving way. It is suitable for forced stripping and removal of a variety of polymer materials, so it is a green processing technology with good cleaning effect.
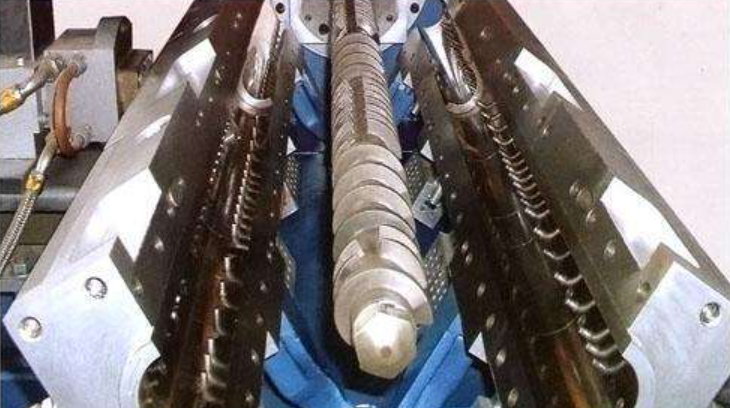
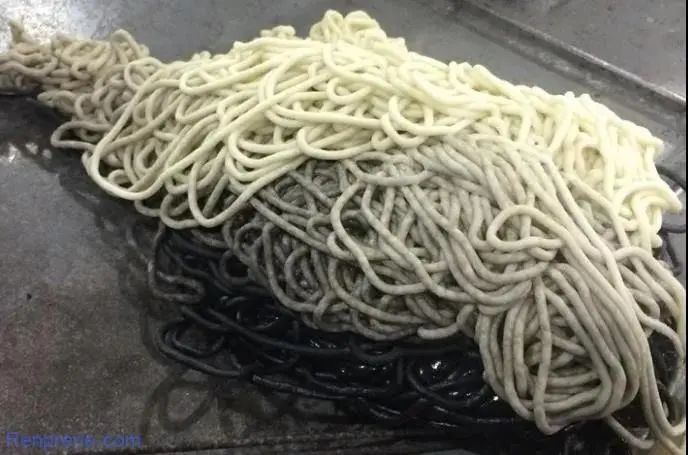
Post time: Jun-07-2024